Mammoth Equipment's Buyer's Guide
Your absolute how-to on exhaust insulation systems, DPFs, and how Mammoth Equipment can help you.
- Exhaust Insulation
- A comparison of the types of exhaust insulation
- What is the best insulation for exhaust surfaces?
- Why do diesel exhaust aftertreatment systems have so many components?
- What do each of the components of a diesel exhaust aftertreatment system do?
- What is regeneration (regen)?
- What is back pressure?
- What is the difference between various engine tiers?
- What is the difference between Tier 4i and Tier 4f?
- Will aftermarket exhaust parts fit my machine?
- The DPF and You
- Equipment & Emissions
- How Mammoth Can Help
Exhaust Insulation
Comparison of the various exhaust insulation types
Exhaust blankets
These are a multi-layer blanket style wrap fitted around the hot surfaces of the system. Layers will often include fibreglass or e-glass insulation, silicon coated cloth, stainless-steel mesh, silica cloth and embossed foil. Typically, these blanket wraps are fastened using hooks and lacing wire, spring clips, or velcro straps. Blankets will be installed as snug around the hot surfaces as possible, often with blankets overlapping each other. This ensures maximum insulation and reduces the possibility of fluid penetration in the event of a spray from a leak from a fuel, coolant, or oil supply line. While blankets are a very cost-effective means of insulating hot surfaces, there is a possible risk of breakdown over time. Many manufacturers seek to make these blankets very easy to install and remove for component inspections, however with the heat and rugged conditions they are exposed to often mechanics will not reinstall if they get removed. Many times, these blankets will be manufactured as an engine or machine-specific kit and available in a few days. Blankets can reduce heat by up to 80%.
- Cost: Medium
- Durability: Medium
- Ease of installation: Medium
- Availability: 2-3 weeks
HTI ceramic hard coating
This is a ceramic baked on coating over fibreglass insulation provided by some manufacturers. These require the exhaust components to be sent away to their factory to be installed. These provide excellent insulation value and are relatively durable in the longer term. Unfortunately, in the event of a component failure (turbo seal, for example) the coating must be chiseled off so that an inspection can be done, the component then must be sent off to the factory again for re-coating which can often take several weeks. Over time it is observed that the coating can let go from the component and rattle. Once it is loose, there is more potential of fluids reaching the hot surfaces in the event of a spray. Ceramic coating can reduce the exterior surface temperature by around 80%.
- Cost: Medium
- Durability: High
- Ease of installation: Poor
- Availability: 6-8 weeks
Silicon-coated fire tape
This is a silicon-coated tape approximately 2-3” wide that is wrapped around the hot exhaust components (typically pipes and mufflers). Relatively easy to install and provides the bare minimum of protection, but once installed it must be cut off to access components. This product is relatively inexpensive and is often available off the shelf. Silicon-coated fire tape will typically reduce exterior surface temperature reduction by around 50 - 60%.
- Cost: Low
- Durability: Poor
- Ease of installation: High
- Availability: Off the shelf
Dual-skin insulated pipe
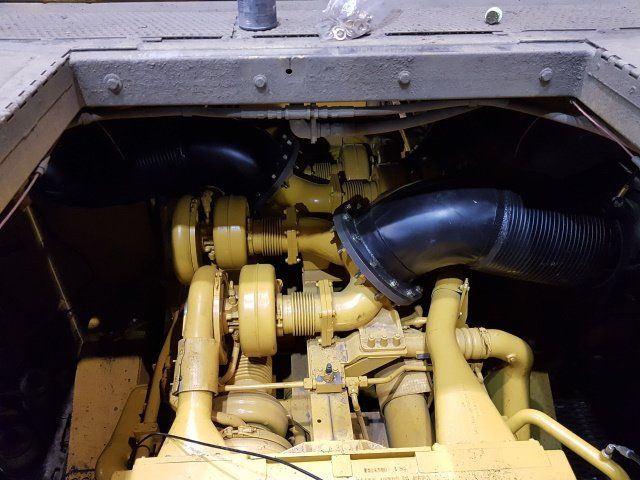
Typically, dual-skins are comprised of 2 skins or layers of steel with 1” of fiberglass between. Some will argue that this is the ultimate for exhaust insulation. When engineered correctly this provides excellent thermal reduction and maximum durability. Some OEM dual-skin pipe systems don’t include the fiberglass insulation between the layers however still provide significant heat reduction of around 70%. These types of systems eliminate the need for additional insulation and will stand up to harsh climates, conditions and pressure washing without concern. They are however the most expensive. Some manufacturers build these systems as a direct fit replacement to the OEM/factory supplied exhaust. Typically, these systems still require some other exhaust insulation around the turbo and manifold for full thermal protection of the hot surfaces.
- Cost: High
- Durability: High
- Ease of installation: High
- Availability: In stock or 3-4 weeks
Embossed foil shields
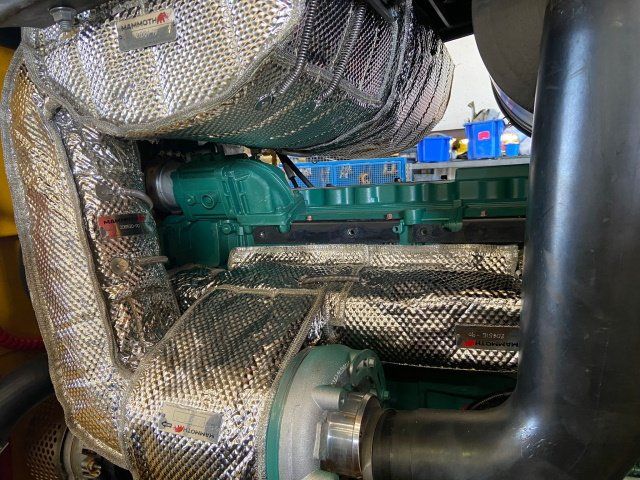
Built using the concept of blanket wraps however with embossed foil on the interior and exterior. These systems are typically built as more of a shield with panels around the hot surfaces, however, are easily installed and removable by being fastened with either spring clips or hooks and lacing wire. The embossed foil provides excellent fluid protection as it is almost impenetrable and is also extremely durable. Embossed foil shields typically reduce heat around 70 - 80%.
- Cost: Medium
- Durability: High
- Ease of installation: High
- Availability: 2-3 weeks
Stainless steel guards
These stainless-steel panels are built as a box around the hot exhaust components to shield them from hoses or wiring harnesses. These provide excellent thermal protection and can often be simple to install. Some of the challenges that can be seen with these types of systems are that they can make access to other engine components more difficult and can develop metal fatigue because of engine vibration. They also tend to be some of the costliest to build of the options.
- Cost: High
- Durability: Medium
- Ease of installation: High
- Availability: 4-6 weeks
What is the best insulation for exhaust surfaces?
This question is difficult to answer as it is influenced by several factors. Where space is available and long-term value is recognized, dual-skin insulated exhaust systems provide maximum durability and are the simplest to install and maintain. If something lower cost is required, then excellent thermal reductions and equipment protection can be achieved for relatively low cost using blanket wraps. It must be recognized that special attention should be made to the fitment and installation of the blanket wraps to ensure a snug fit and to reduce the possibility of fluid penetration from hose leaks or pressuring washing where blankets meet. The Mammoth 6000 and 8000 blanket wraps are designed often from a 3D scan of an engine or exhaust system, and this allows for the system to be developed as a very snug fit considering for other nearby components.
As emissions regulations have become stricter, exhaust aftertreatment systems have become more complex. Some of the common components found on many Tier 4 and higher engines are:
- Diesel Oxidation Catalyst (DOC)
- Diesel Particulate Filter (DPF)
- Selective Catalytic Reduction (SCR)
- Ammonia Slip Catalyst (ASC)
- NOx sensors
- Diesel Exhaust Fluid (DEF) Dosing module
Each component is required to address a specific area of diesel emissions that the system is seeking to improve.
- DOC - the Diesel Oxidation Catalyst is typically the first component in any exhaust aftertreatment system. Its purpose is to capture oxygen molecules and attach them to other gases passing across it. Primarily we see toxic CO (Carbon Monoxide) get converted into CO2 (Carbon Dioxide). Many DOC’s will reduce CO by 90% which is excellent for reducing the toxicity of diesel emissions. We also often see some NO (Nitric Oxide) be converted into NO2 (Nitrogen Dioxide). While NO2 is not desirable it is required to enable a DPF (Diesel Particulate Filter) system to regenerate soot into ash. While some exhaust aftertreatment systems will cause increases in NO2 some passive DPF systems will cause a NO2 reduction at some engine operating points.
- DPF - the Diesel Particulate Filter is the generic name given to the complete exhaust aftertreatment system. This is not correct as it relates only to the soot filter section. Typically, this is found directly after the DOC. This filter is often built from a porous ceramic material (Cordierite or Silicon Carbide). The filter itself is built looking like a honeycomb of square tubes. Half of these tubes are blocked off at the inlet side and half on the outlet side. This forces the exhaust to pass through the side walls of these tubes. As the exhaust passes through the porous side walls of these tubes the diesel particulates (soot particles) are captured. It is in the DPF that the soot is regenerated from being heavy and dense into light and low-density ash. This filter will become plugged or loaded over time with the ash and will require cleaning to ensure the back pressure on the engine doesn’t become too high.
- SCR - the Selective Catalytic Reduction operates by injecting and spraying/dosing the exhaust with DEF (Diesel Exhaust Fluid) which is a urea-based fluid. After the DOC and DPF have reduced the soot (DPM, diesel particulates) the remaining emissions of concern are the NOx gases, the combined NO and NO2 gases. The combination of the DEF dosing and the SCR catalyst causes the NOx gases to be separated into primarily nitrogen and water vapour.
- ASC - the Ammonia Slip Catalyst further separates any remaining ammonia into nitrogen and water vapour. Some SCR systems will require an ASC. This recognizes that there may be higher than desirable levels of ammonia leaving the SCR.
- NOx sensors - all aftertreatment systems with SCR will require NOx sensors. There will need to be a sensor before and after the aftertreatment system to measure the delta between NOx in and NOx out. A calculation is done on the difference in NOx levels to determine the amount of DEF fluid the exhaust needs dosing with.
- DEF dosing module - based on what the NOx sensors are reading, a calculation is done on how much DEF fluid should be injected/sprayed on the exhaust. The DEF dosing module is a unit that includes both a pump and a spray nozzle and is responsible to spray the DEF fluid on the exhaust between the DPF and SCR. Typically, 24” – 30” of exhaust tube is required, including mixing baffles to ensure the DEF fluid is properly mixed with the exhaust and the desired reaction occurs.
Diesel particulates or soot in diesel exhaust are heavy, dense, and oily. Passed through a filter they would quickly plug up the filter. Regeneration is the process of igniting this soot and ‘baking’ it down into ash (light and low density). Soot would typically need to be heated to 1,112 F° to ignite, however with a DOC this can typically be lowered to around 600 F°. While it would be dangerous for diesel exhaust to reach temperatures of 1,112 F°, 600 F° is often reached when the engine is under load. This means that the heat from the exhaust on a diesel engine can regenerate the soot into ash by itself on many machines, known as passive regeneration. For equipment that is not run under load frequently like light vehicles such as school buses or delivery trucks that may do a lot of stop and go, it is necessary to have an active regeneration system. With an active regeneration system there is an external heat source like an electric heater or a fuel line with an ignition system to heat the DPF up to the required regen temperature.
High back pressure will cause the turbo to spool up slower and restrict the normal working of engine valves. As the DPF filter becomes loaded either because of soot loading or ash build up it will cause a restriction on flow. This restriction will cause a pressure in the exhaust system to back up towards the engine. Operators of vehicles with high back pressure will quickly complain of low power. Running a vehicle with high back pressure for too long will likely cause engine component failure because of the sustained strain on the turbo and valves.
Until 1997, there were no real diesel emission regulations to note. Tier 1 was introduced in 1997 and this set tailpipe limits on DPM and NOx gas levels. In proceeding years, Tiers 2, 3, 4 (interim and final) have been introduced. We are now seeing some further emission tiered engines arrive in North America such as Stage 5 and Euro 6. With each tier, the requirements for DPM and NOx levels have reduced as we moved to ‘near zero’ emissions.
In 2012, Tier 4 diesel emissions requirements were introduced. Initially this came out as Tier 4i (interim) as the major reduction from Tier 3 was in DPM (diesel particulate matter) resulting from the addition of a DPF on most engines. In 2015, engine manufacturers were able to introduce Tier 4f (final) engines that massively reduced NOx emissions from adding SCR technology behind the DPF in the aftertreatment package.
Yes! At Mammoth Equipment, we take great care to reverse-engineer exhaust components from original factory installed parts. This ensures the parts are a direct fit replacement to the OEM for easy and quick installation. Each part has been critically scrutinized to evaluate failure points on the factory components and to ensure the parts we build will last longer and lower equipment downtime for equipment operators.